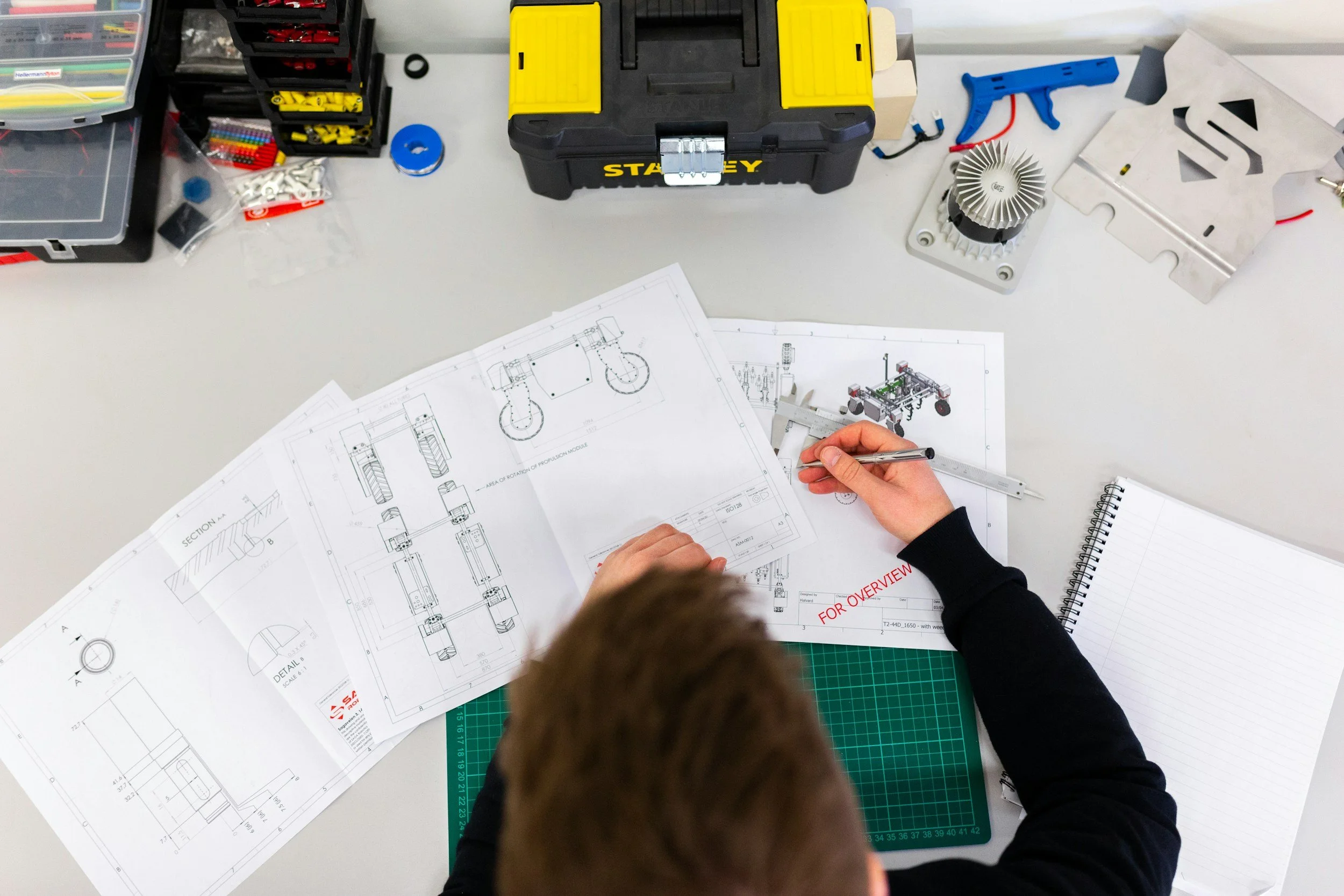
FSAE EV Formula Car: Formula Buckeyes
Mechanical Engineering Capstone Project
Dual Motor Subsystem
Drive-train Subsystem
Conclusion
A sensitivity test was run on the Simulink model showing which variables have the largest effect on 0-60 MPH time.
0-60 MPH is 4.67 seconds
Baseline variables for the EV are based on Wisconsin’s WR-217e Architecture (https://www.wisconsinracing.org/wp-content/uploads/2020/10/WR
Colleges nationwide compete in a yearly Formula Society of Automotive Engineers competition (SAE). In this competition, each school's mechanical engineering department builds a smaller model of a Formula 1 car and takes it through several tests like acceleration speed, braking efficiency, and cost analysis.
Project Aim
Using a Simulink project allows for the EV to be simulated in a physical environment. This environment is controlled by a MATLAB script file that sets all variables of the vehicle and environment. This file is easily editable to be flexible for users.
Results
Phase I: Develop a Low Fidelity model which comprises of a Kinematic study of Vehicle Parameters using MATLAB.
Phase II: Develop a High-Fidelity model using Simulink that appropriately simulates an SAE Formula EV car. The Simulink Project also includes an additional MATLAB File that consists of all vehicle parameters.
Future Work:
Future work in this field would include a deeper dive into the battery and controller subsections of the model. The battery gives enough power and voltage to not cause issues to the rest of the system, while the motor controller begins to limit speed at around 70 MPH. Finally, lay the groundwork to provide Formula Buckeyes with a Electronic model for developing an SAE EV powertrain.
0-60 time:
• Increases with increasing vehicle mass, drag coefficient, and frontal area
• Decreases with increasing torque and center of gravity height
It should be noted that unphysical effects occur when variables are tested outside the 90% - 110% range.